We had a nice a sunny day today which helped greatly to keep the momentum going with everything that has to be loaded on board. Especially with the loading directly from the container to the ship. Nobody likes getting wet while unloading and not everything that is unloaded has been protected and packaged in such a way that it can survive standing in the rain on a dock for a prolonged time. So we take every bit of dry weather as a blessing and a bonus.
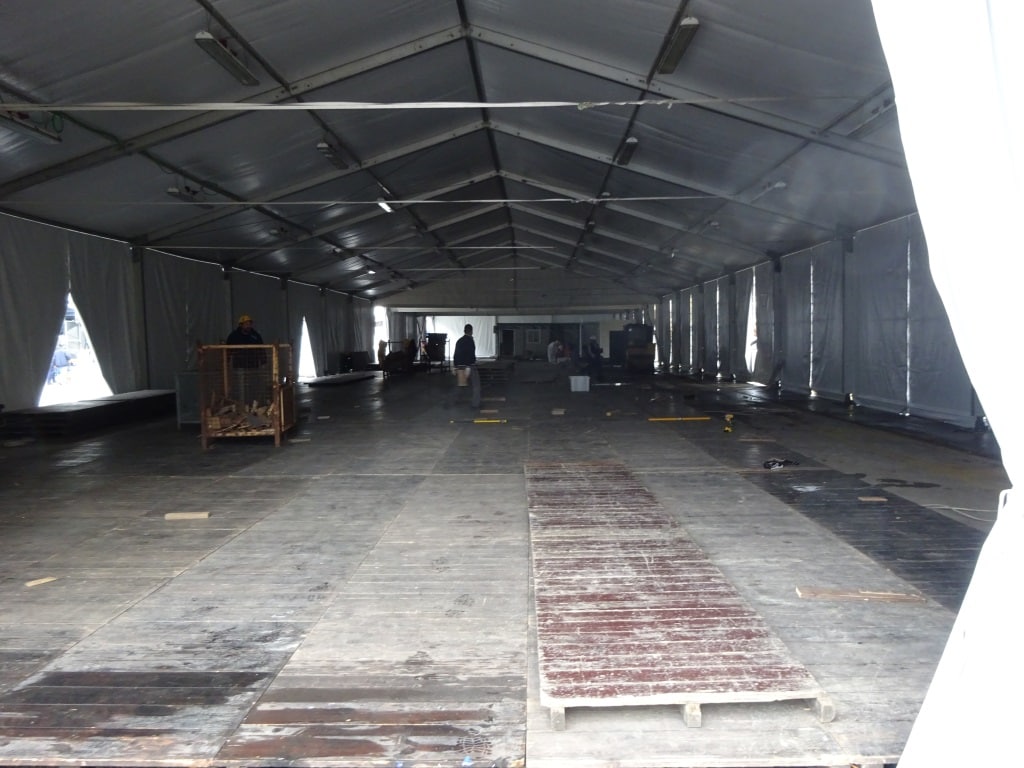
Not a bad seize as far as a tent goes.
We have only 22 days to go to sailing date and even less to the handover as that is planned for the 29th. Then on the next day we sail for Venice to get the ship ready for the Shake Down Cruise which will start on the 1st. As the hand over is a very elaborate happening, the yard is already building a large tent just outside the ship for everybody who is involved in the proceedings. Apart from that there is also a day that the yard people can bring their families on board to show them the ship they have been working on. Some of them from the start of the building process. You would almost think that with so many ships being constructed here, they could leave the thing here permanently but I suppose if you want to have the tent (or marquee to use the posh word) close to the ship, then it has to go up and down with every delivery. It simply would take up to much valuable space for the construction.
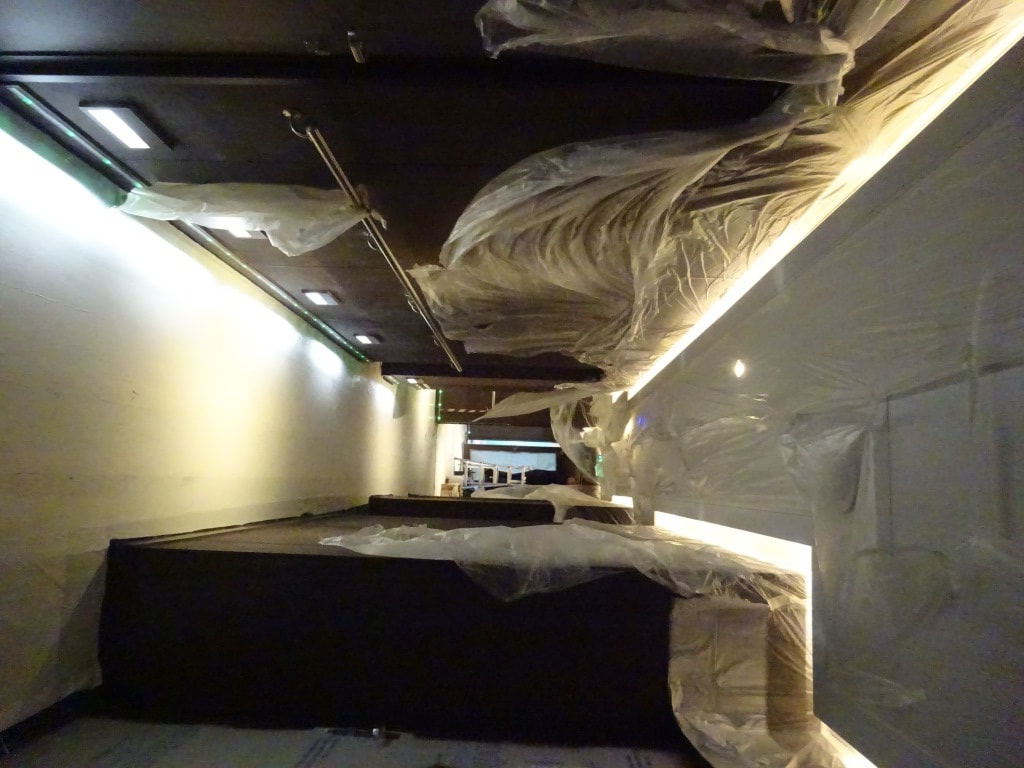
A belated Halloween on the Nieuw Statendam with the Ocean Spa as haunted mansion.
Walking around the ship is still a confusing happening at times. Although a lot of wires, pipes and cables have been cleared away, there is still tile setting going on, some carpeting and laying of tiles and wood. This means that there is no walking from bow to stern in the straight way that the guests are able to do. Everywhere (Fire screen) doors are closed blocking off half the passage way or completely if there is another door out. This is done by the Sub Contractors working in a specific area to keep other workers from stepping over their latest handiwork. There are shipyard fire patrols roving over the ship and one of their duties is to ensure that the emergency routes are being kept clear to at least a certain extent in case something happens. Thus I was able to witness a rather heated conversation between a fireguard protecting the safety of the ship and a contractor trying to protect his flooring. The fireguard of course won the argument and work had to continue in 2 stages. At the same time they try to protect everything they have finished until ALL the work is finished and there is no danger of further damage. This made the corridor in the Spa area look like something especially rigged up for Halloween. Only the flickering candles and a witch or two were missing.
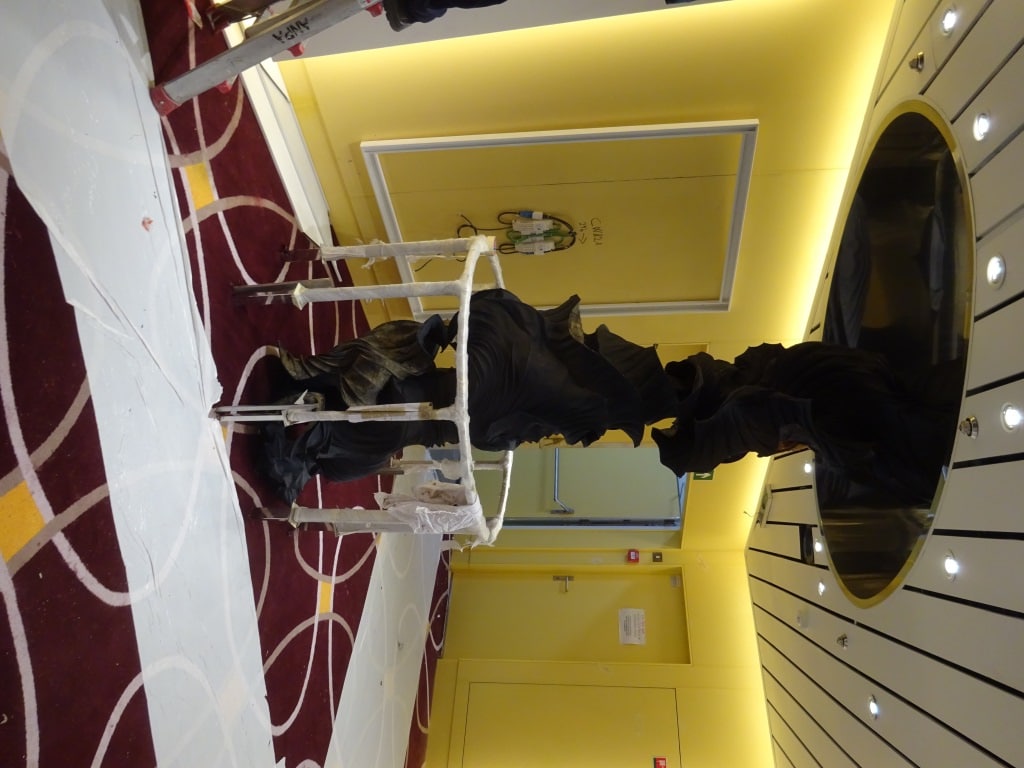
Sb Forward Dining room. What the Koningsdam has in white, we have in black.
The first pieces of art have arrived, although the major pieces which are in the way of the yard traffic will come later. But the large sculptures in the Queens Lounge and Dining room that go up over two decks are already in place plus a few tentative framed photos in the Photo Gallery which has been completed apart from the Technical equipment. Layout of the dining room is the same as on the Koningsdam with the except that what was white on the Koningsdam is black on the Nieuw Statendam.
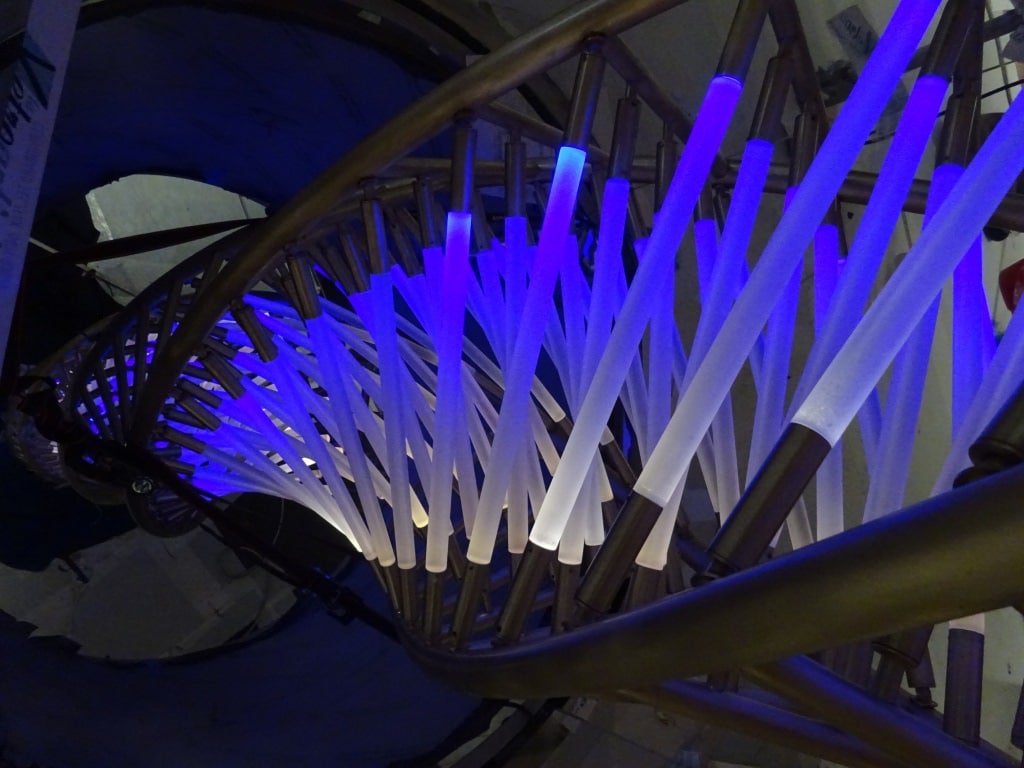
The sculpture aft of the Queens Lounge / BB King Jazz Club. It also rises up through the deck in a sort of DNA string form.
I hate it when I am not clear in my descriptions of what is going on. But to answer a query on the blog. Deck 2 has the Music Walk. And it is the main public room area after the Main Stage. The port side is Billboard on Board with the dueling pianos. This area is separated by a winding staircase which goes to deck 3 (casino area). The right hand side of the space was in use by the Lincoln Art Center and more or less wasted after their last performance. Here is where the Rolling Stone Rock Room will be situated. The overflow of guests can sit/stay in the Billboard on Board area and vice-versa, depending on who is playing. Lincoln Art Centre is moved to the Queens Lounge. Here we had “wasted hours” as well as BB King only starts at 21.00 hrs. in the evening and that is the time that Lincoln Arts normally finishes anyway.
Tomorrow will be another day and I am predicting another sunny day. Seems to work, I was right today.
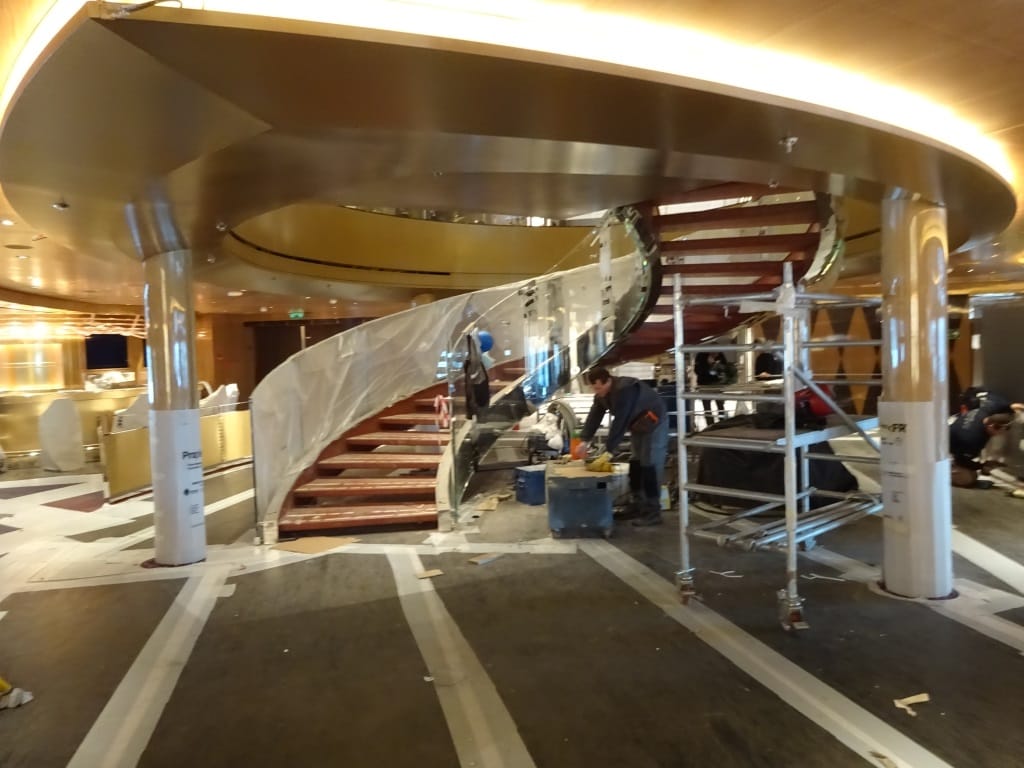
The rather iconic staircase which leads from Deck 2 up to deck 3. It sort of divides the space in two while still making it possible for the guests to see everything.